GREATER STRENGTH MEANS GREATER PRESSURE INTEGRITY.
COMPARE THE PRESSURE BETWEEN THE OLDER NOZZLE HARDWARE VS A CLICK&DRY™ SPRAY DRY NOZZLE
The Click&Dry™ design makes safety and pressure integrity its number one design priority. Since the early 1970’s, high volume powder production has seen the emergence of nozzle type dryers as a major developing trend, resulting in steadily increasing operating pressures to achieve the volumes and consistencies required. This placed enormous demand upon
pre-existing nozzle hardware designs, which over time has essentially remained unchanged. Today, it is not readily shown that this hardware is operable without significant risk and within accepted safety factors now dictated by modern industry.
Spray Nozzle Engineering has studied many types of dryer nozzle hardware in use today. The initial findings of this study were that a generic form of nozzle design has been in common use for some considerable time, from a number of different sources, with most utilising radial seals and very similar hardware geometry. It was also determined through analysis in this study, that a large proportion of such equipment reviewed may operate far in excess of industry accepted stress and pressure limits due to this observed generic geometry and radial seal arrangements. Further, that much of this hardware exists in a worn or old and fatigued condition, which alone, poses a high risk of failure. Click&Dry™ was developed to function within a range of operational safety factors which far exceed that of current competitive equipment in the field, with unique high pressure axial seals, as well as a design that resists the normal types of observed wear characteristics of older style nozzles in service.
Industries working with pressure systems and vessels, typically stipulate a safety factor of 2-2.5 times based upon the yield stress of the material in use. If operating at a safety factor below 2, a thorough understanding of your fatigue cycles and the potential failure risk is critical. Operating at safety factors approaching 1 or below, ensures failure is imminent based upon known engineering protocol and the properties of typical materials used. This is why Click&Dry™ components are designed around important pressure related standards such as ASME B31.3. These standards are dedicated to safe operation of pressure systems and provide safety margins that exceed those in current use based upon the yield stress and other important factors.
World Wide Sealing Standards all dictate the use of backup rings in the typical radial seal arrangements found in most common dryer nozzles. Widely adopted global standards typically call for pressure limits of around 100barG without backup rings. One exception is JIS B2406 seal standard which still limits the working pressure without backup rings to only 255barG, this only being achievable with enormously tight radial gap and costly higher duro-rated O-rings. It is clear most modern dryers operate far in excess of these pressures and as such require a more reliable and compliant sealing option. Click&Dry™ axial seal arrangement allows for greater operating pressures with no need for expensive backup rings and high duro-seals. This is good news for dryer operators in managing operating costs of daily seal replacement.
It can be seen from the review summary below, that many common older spray components in use today operate at pressures far exceeding their yield stress, with a risk of failure, being extremely high. Operating this older equipment at this level is not recommended. This review chart provides the customer with a range of notional safety factors to help them identify the level of operational risk they currently choose to adopt.
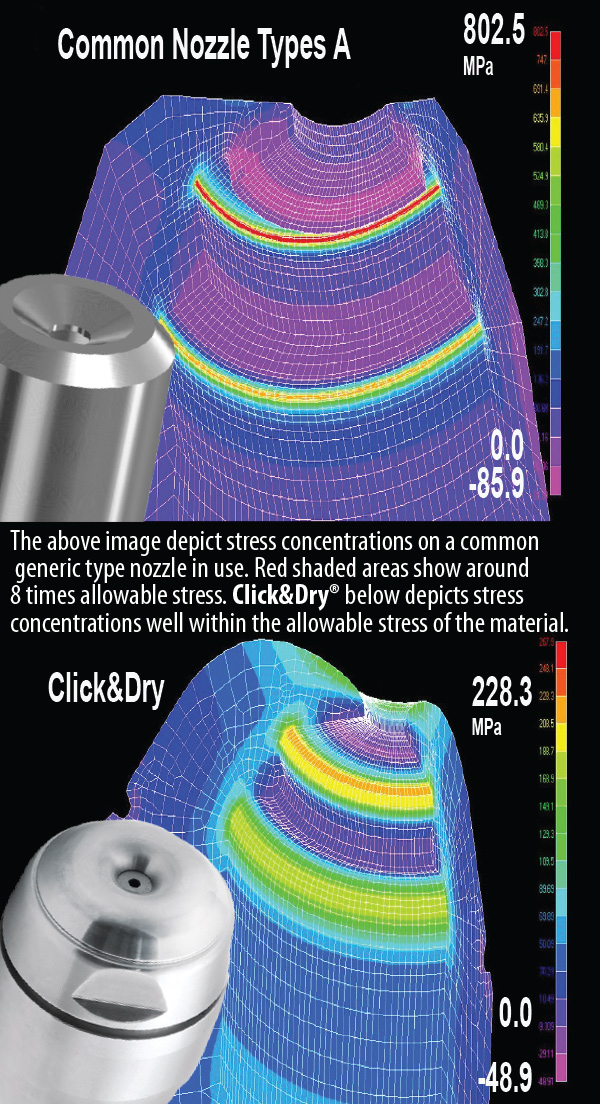

A STRONGER CHOICE
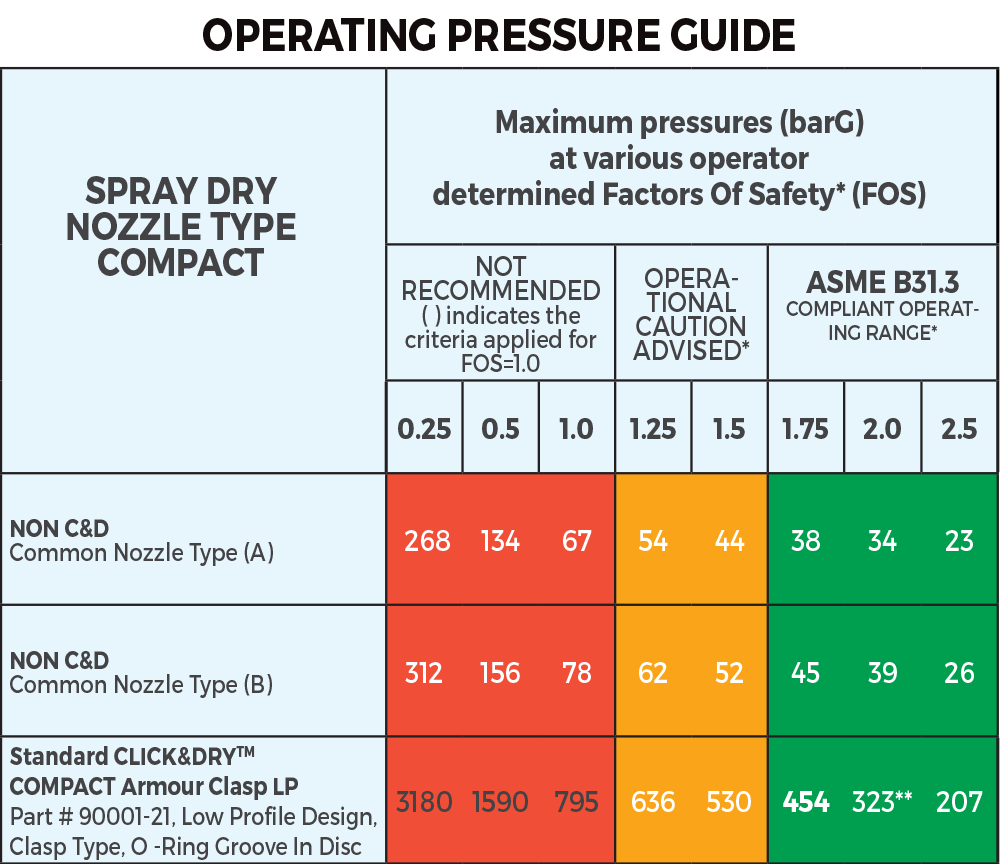
Notes *
- Applies to 350barG at 20-220degC before pre-load (cap torquing) and no other loads, fatigue life of approx. 20,000 cycles.
- The ASME compliant pressure range as per the green coloured section.
- Data represents scaled stresses not fatigue life, as FOS is based upon Factor of safety for all failure modes and yield strength is the primary mode for most scaled loads (ie. because fatigue needs the actual stress to estimate the fatigue life and double fatigue life typically occurs at -20% stress, whereas -20% on yield is an FOS of 1.2 not 2.0 for fatigue).
- A minimum FOS in pressure vessel design is 2-2.5, what is inherent in the ASME B31.3 is approximately 1.3-2.0.
- Notional fatigue life of at least 5000 cycles factor of safety based upon internal design pressures & minimum yield stress & minimal pre-load.
- **Indicates ASME B31.3 compliant pressure for design at 220C.